Be kind, re-wind: Can wind turbines be recycled when they retire?
Be kind, re-wind: Can wind turbines be recycled when they retire?
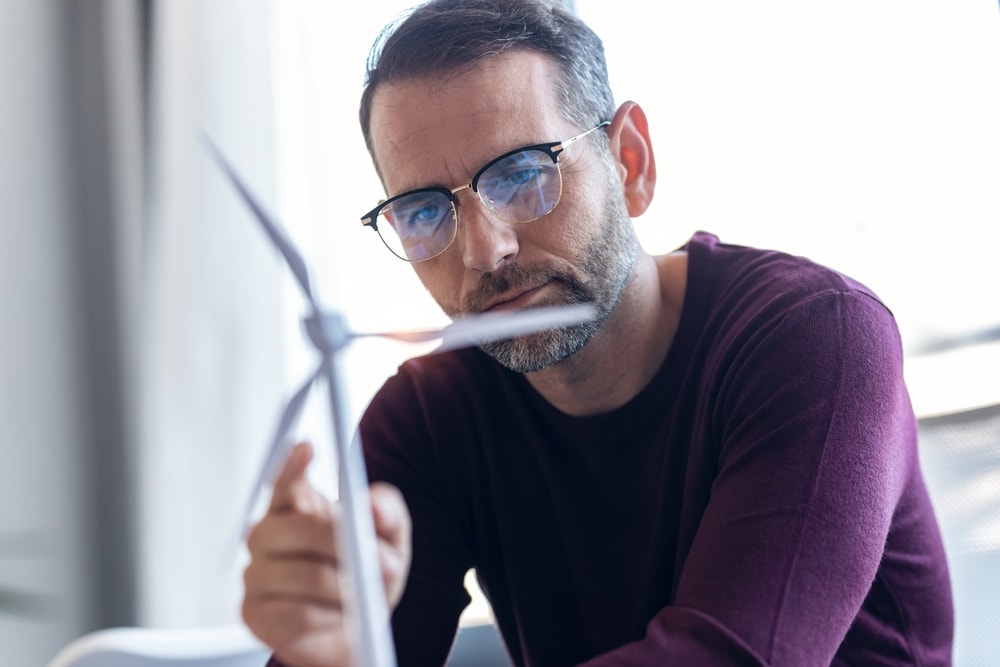
Wind energy is critical to our clean energy future. As the world moves towards net zero emissions, and Queensland targets 80 per cent renewable energy by 2035, wind turbines are becoming an increasingly common sight – but what happens to those turbines when their blades stop spinning?
Wind energy is a clean and sustainable alternative to fossil fuels. It’s produced by wind turbines, which convert the natural movement of the air into mechanical energy through the rotation of turbine blades. A generator in the turbine’s nacelle converts this mechanical energy into electricity, which is sent to the electrical grid.
Wind turbines don’t emit greenhouse gases, fine particle pollution, sulphur dioxide or nitrogen dioxides. They’re usually grouped together in wind farms, which require very little water during operation, and don’t pose a significant risk of groundwater pollution.
As a renewable, environmentally friendly energy source, wind is set to play a key role in decarbonising our energy mix. In Queensland, which has some of Australia’s highest wind speeds, more than 2,000 new turbines are expected to be built by 2035 in order to reach the State Government’s renewable energy targets.
But while the current focus is on installing the wind and solar capacity that’s necessary for our clean energy transformation, it’s also important to consider what happens to these projects at the end of their life.
Spin cycle: The life cycle of a wind farm
Wind farms typically have a life cycle of 25 to 30 years, and as long as they’re properly maintained, most turbines will remain highly efficient throughout these years. If the turbines are still in excellent condition at the end of the farm’s ‘design life’, then it’s possible for them to be re-permitted so the farm can continue to operate.
The owner can also partially repower the wind farm by overhauling, optimising or upgrading components of the existing turbines (specifically the nacelles, rotors and blades); or fully repower it, which essentially means building an entirely new facility on the same site.
The final option is to decommission the wind farm. Decommissioning means removing the wind turbines and all ancillary infrastructure, and rehabilitating and revegetating the site, so the land can be returned to its former use.
Decommissioning is the responsibility of the owner of the wind farm, not the landowner. Generally, development approvals and contracts with landowners will contain clauses spelling out the expectations and time frames around decommissioning the wind farm and rehabilitating the site.
When a wind farm is decommissioned, the turbine components have to go somewhere. And with some of Australia’s oldest wind farms now reaching the end of their life, this has become an increasingly topical issue.
In 2023, the Clean Energy Council released a report into the decommissioning and waste management of Australian wind farms, which examined the options available to owners.
Recycling
The report found that between 85 and 94 percent of a wind turbine, by mass, can be recycled, surpassing the National Waste Policy Action Plan's average resource recovery rate target of 80 per cent across all industries by 2030.
This high recovery rate is primarily due to the recyclable metals used in turbine construction, such as steel, aluminium, copper, and cast iron. Australia has a robust scrap metal recycling industry, and the steel towers, copper cabling, and aluminium components that make up a wind turbine can be readily recycled in steelworks and foundries.
However, turbine blades pose a significant recycling challenge. While the exact material composition varies between wind turbine designs, they are generally made of epoxy and composite materials like fibreglass or carbon fibre. The strong bond between these materials that enables them to withstand strong winds also makes them difficult to recycle.
The most common method currently used is mechanical grinding, which processes the composite materials into short fibres and ground matrix (powder). While effective and low-cost, this method produces recycled products that are less valuable than the original materials. The shredded material can be used as fillers in construction or manufacturing, but sustainable recycling requires clear, secure end markets, which are still developing.
Innovative recycling methods are emerging. For instance, Vestas has developed a chemical technology to break down epoxy resin into virgin-grade materials, potentially enabling a circular economy for turbine blades.
Other methods include pyrolysis, which recovers fibres from the resultant char product that can be resold at a competitive price; fluidised bed combustion, which recovers reinforcing fibres; and solvolysis, which uses solvents to break down resins and recover fibres – the success of which is dependent on the type of resin used in the blades.
Aside from coming up with better ways to recycle existing turbine blades, the industry is also developing new blades that can be more easily recycled. Manufacturers are developing blades using new types of resin that can be chemically separated from other components, allowing the materials to be reused.
As the number of decommissioned wind farms increases, it’s expected that more recycling options and innovative solutions will continue to emerge.
Repurposing
Repurposing involves using the original engineered structure and properties of an object for a new, different purpose that requires less processing than recycling.
The Clean Energy Council report notes that wind turbine blades have been repurposed for several alternative functions. For instance, in Europe, blades have been transformed into bus stops, playground equipment, and public seats.
The Re-Wind Network, a research partnership of Irish and American universities, has developed a catalogue showcasing designs for various structures and products made from repurposed wind turbine blades, including bridges, poles, sound barriers, roofs, and farming equipment. This repurposing approach avoids the need to use new materials to build these structures, supporting a circular economy.
However, the report notes that scaling these alternative uses to commercial production remains challenging, and isn’t necessarily sustainable. The main barriers to repurposing include perceived lower quality of used materials; unknown residual structural properties; a lack of established end markets; and unpredictable material availability.
Recovering
One of the primary methods for making use of wind turbine blades and other composite waste at the moment is through cement co-processing. This is referred to as ‘energy recovery’, rather than recycling, because the technique involves using the polymer matrix of the blades as fuel in cement production.
This process is currently being implemented by wind farms in Germany, where it has reportedly been effective, scalable, and cost-efficient, but it is energy-intensive, and is currently limited to fibreglass blades and not carbon fibre.
Ultimately, as the sheer number of turbine blades reaching the end of their life increases, economies of scale will make recycling them more viable. With ongoing industry collaboration, research and development, the wind industry can address the challenge of managing composite materials, and move closer towards a truly circular economy.
Subscribe to our newsletter
STANWELL SPARK
Stay up to date with quarterly news from Stanwell, delivered straight to your inbox. Learn more about our projects, partnerships and how we're delivering affordable, reliable and secure electricity for Queensland.