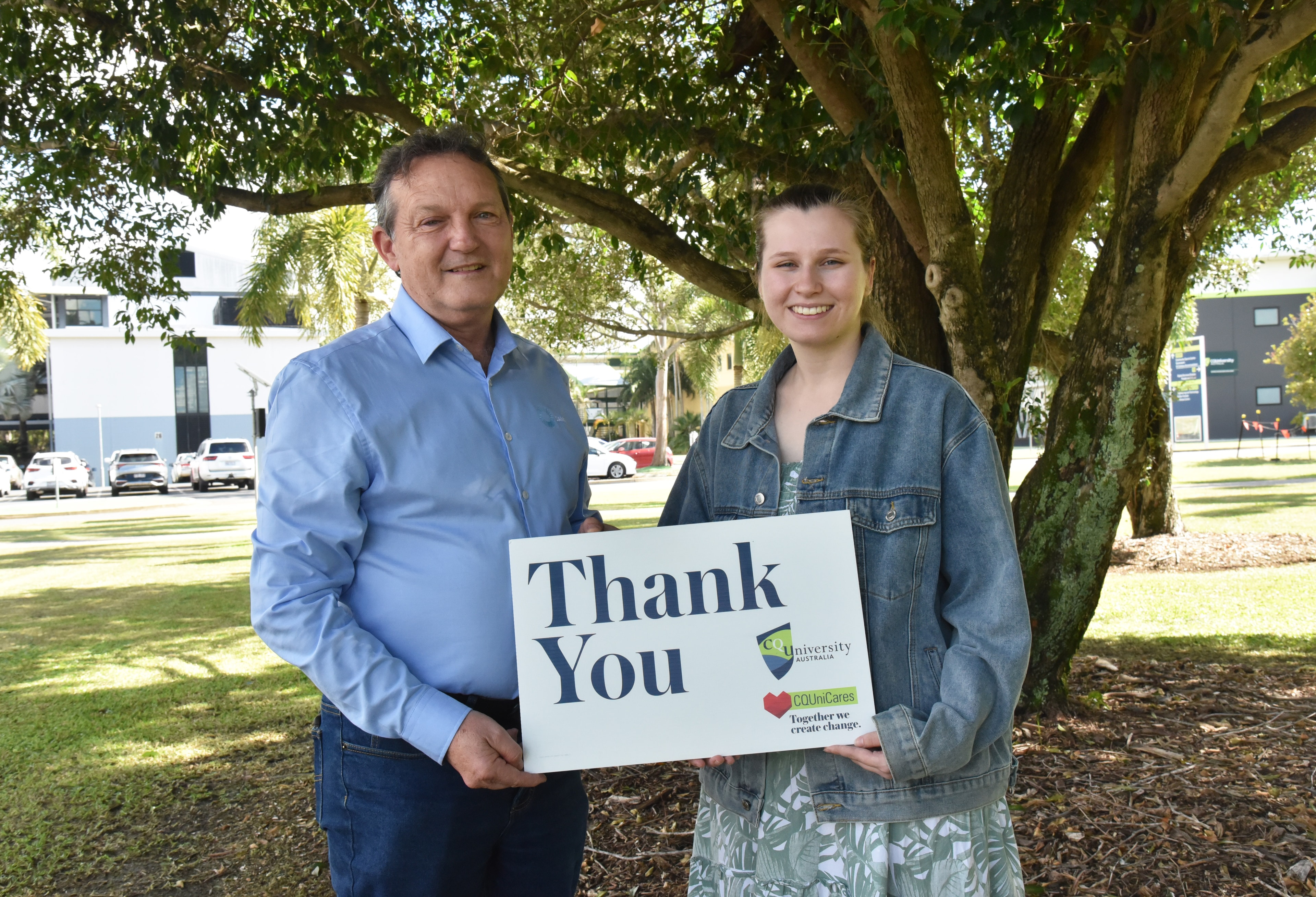
- Articles
- Asset Maintenance
- Communities
Supporting tomorrow’s leaders: SAMCo backs CQUniversity student on her path to healing and higher education
SAMCo supports CQUniversity student Kalyna Markwell with a scholarship to pursue psychology and give back to First Nations communities.
29 June 2025